Properties of Portland Cement
In the realm of specifications related to Portland cement, there is a notable focus on regulating its chemical composition and certain crucial physical properties, as indicated by the guidelines in the NTC 121 and 321 standards. In this context, it is essential to appreciate the importance of understanding these properties as they significantly influence the accurate interpretation of the results obtained from the tests to which the cement is subjected.
Setting: What is it and how does it work?
The setting of Portland cement refers to the chemical and physical process by which a mixture of cement and water changes from its initial liquid or plastic state to a solid and cohesive state. This process is essential in the formation of concrete and mortar since it establishes the transition from a moldable substance to a solid structure with mechanical strength.
Setting is a multifaceted process involving various chemical reactions and changes in the microscopic structure of the cement components. Immediately after mixing with water, the reactive compounds in cement, such as calcium silicates (C3S and C2S) and calcium aluminates (C3A and C4AF), begin to hydrate. During this hydration, the ions released by these compounds combine with water molecules to form hydration products, such as hydrated silicates and aluminates, as well as calcium hydroxides.
As these hydration products develop, the cement paste undergoes a change in its physical state and properties. In the initial stages, the paste becomes viscous and gains cohesion, known as “initial setting.” This initial phase is crucial for the handling and placement of the material in construction.
Over time, the hydration products continue to develop and form a three-dimensional crystalline network within the paste. This leads to a gradual increase in the material’s strength and stiffness. The point at which the paste reaches sufficient strength to withstand additional loads marks the “final setting.” At this stage, the paste has transformed into a solid and coherent structure capable of resisting mechanical stresses and external loads.
The setting process of Portland cement is influenced by various factors such as the cement’s composition, water-cement ratio, ambient temperature, and humidity. Understanding and controlling the setting process are crucial to achieving proper handling of the material during construction and ensuring that the constructed structures acquire the desired strength and durability over time.
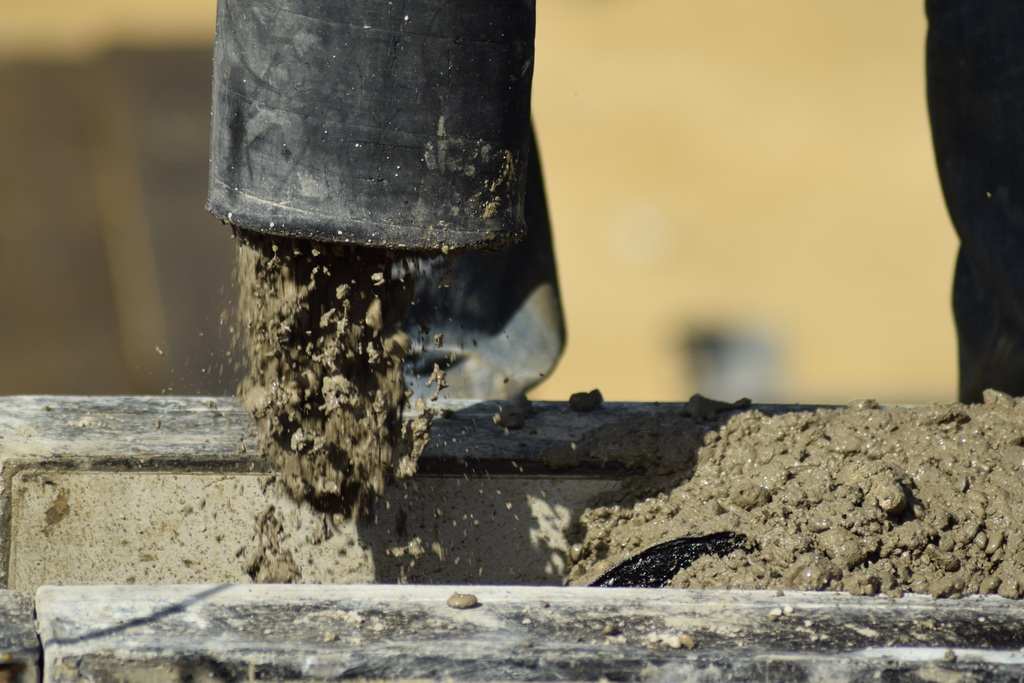
False Setting: Learn to Recognize It
False setting is an effect that every architect and civil engineer must be aware of in the context of Portland cement. It refers to an abnormality that occurs in the early stages of the hydration process, in which the mixture of cement and water acquires an unusual and premature stiffness. This is characterized by the early loss of plasticity and malleability in the freshly mixed cement paste, giving the impression that the material is setting when, in fact, it is not. It is important to note that false setting is different from flash setting, which involves true setting but in an exceptionally short period.
This phenomenon of false setting is manifested by a sudden decrease in the workability of the mixture, accompanied by a limited generation of heat. In other words, the cement paste begins to become stiffer and less malleable shortly after the addition of water, even though there has been no significant hydration of the cement compounds.
A distinctive feature of false setting is that if the hardened paste is re-mixed without adding more water, it regains its workability and can set normally without losing its ability to gain mechanical strength. However, if the process continues without regaining workability and starts to release heat appreciably, it is considered to have undergone true setting but in an exceptionally short period.
In construction projects, pronounced false setting can create difficulties in handling and placing the cement mixture, especially in situations where the mixing is done for short periods and transported without efficient agitation. However, in circumstances where concrete mixing extends over time, such as in mixer trucks or when re-mixing before placement, the effect of false setting tends to be less problematic.
To prevent or mitigate false setting, it is essential to carefully evaluate the cement composition and the water-cement ratio, as well as consider the environment and mixing conditions. With a solid understanding and proper management, construction professionals can minimize the negative impacts of false setting and ensure efficient handling and placement of cement in their projects.
Cement Density
In the world of civil engineering and construction materials, one of the crucial aspects to consider is the density of Portland cement. This property typically exhibits a range of variability from 2.90 to 3.20 g/cm3. This variability is greatly influenced by the quantity and density of pozzolanic materials incorporated into the cement during its production.
It is essential to highlight that while density is an important factor, it should not be taken as a direct indicator of cement quality. Instead, its primary role lies in two fundamental aspects: precise dosing in mixes and rigorous control of the mixing process. The relationship between density and quality is more complex, where other factors such as strength, durability, and setting characteristics are also key determinants.
The typical method for evaluating cement density involves using the Le Chatelier flask, following the technical standard NTC 221. This ingenious flask allows for the measurement of the volume corresponding to a fixed mass of cement (usually 64 g) by displacing a liquid contained inside it. It is important to note that the liquid used in this procedure should be water-free kerosene or naphtha with a gravity of no less than 62o API. The choice of this liquid is based on the need to avoid premature initiation of hydration reactions in the cement, which would result if water were used.
Fineness of Its Particles
This property, closely related to strength development and heat release, presents a complex interaction that deserves a detailed analysis.
The fundamental role of fineness in cement lies in its ability to directly influence the strength it can develop. It is a known fact that the finer the cement, the greater its capacity to achieve optimal strength. However, this increase in strength is accompanied by a more intense heat release. Understanding this relationship is in the distinction between coarse and fine particles in the hydration process.
Coarse cement particles can persist for years without fully hydrating, leading to suboptimal strength. In contrast, fineness plays a crucial role in maximizing the amount of material that hydrates. This is because, with finer cement, the total surface area in contact with water increases significantly. This increased interaction between cement and water leads to broader hydration of the total mass of cement, resulting in higher desired strength development. However, it is important to note that this intensive hydration also generates a proportionally higher heat release.
The measurement of fineness is carried out by determining the area of the particles present in a unit mass of the material, a parameter known as “Specific Surface.” Typical units for this measurement are cm2/g or m2/kg. The evaluation of fineness in cement can be done through various methods. Sieving, following technical standards NTC 226 or 294, is one option, allowing for classification by particle size. In addition, the Blaine permeameter (NTC 33) and the Wagner turbidimeter (NTC 597) are also preferred tools for determining fineness, providing valuable information to ensure the quality and performance of cement in engineering applications.
Normal Consistency
A critical property that requires careful attention is the normal consistency of cement paste, a factor that directly impacts key properties such as setting times and volumetric stability.
To achieve a precise understanding of cement properties, a crucial process is carried out: the creation of a mixture of cement and water, known as paste. Since the characteristics of this paste are influenced by the precise proportions of its components, it is necessary to prepare a “normalized” paste that reflects optimal hydration of the cement. This paste is called “normal consistency paste.”
The determination of normal consistency paste is carried out following the guidelines established by the technical standard NTC 110, a rigorous procedure that allows for an adequate level of precision. The test involves identifying the water proportion in relation to the mass of cement used, typically 500 g. The goal is to place this paste in the “Vicat” device, a probe with a diameter of 1 cm and a total mass of 300 g, which penetrates the paste to a depth of 10±1 mm within 30 seconds. This depth and penetration rate are key indicators of the desired consistency.
In practice, the water percentage in normal consistency paste tends to vary in a range between 23% and 33% with respect to the mass of cement used. This variability allows for adjustments in the paste properties to make it representative of actual use conditions, enabling optimal hydration and performance.
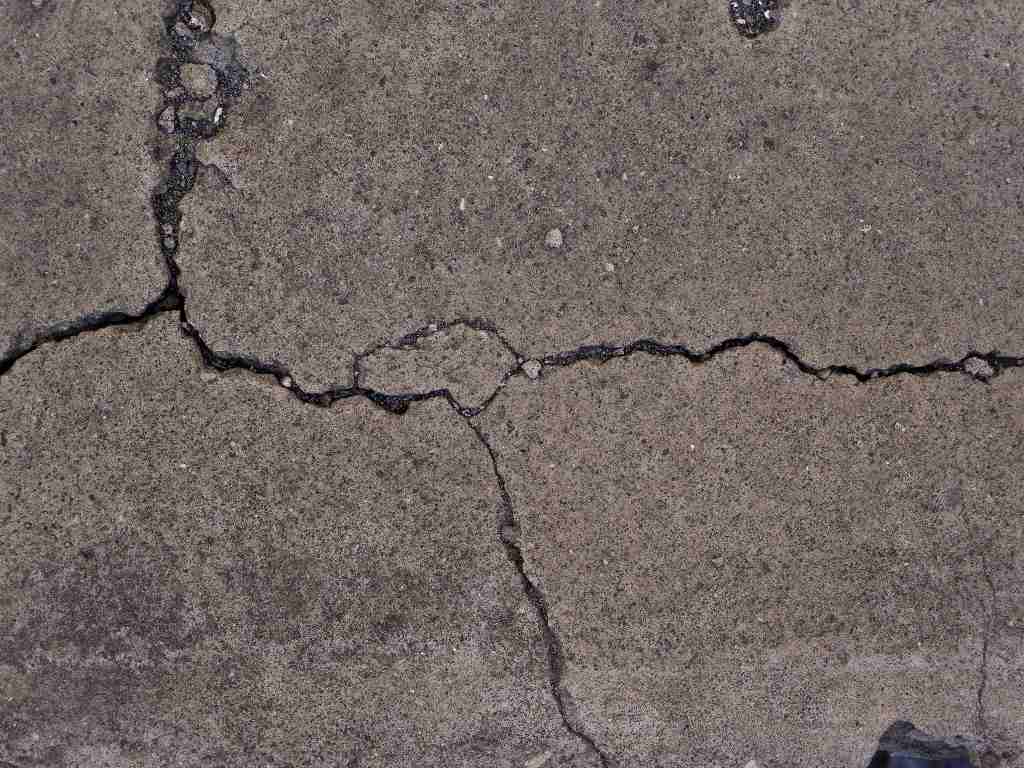
Heat of Hydration in Portland Cement
The term “heat of hydration” refers to the thermal energy released during the hydration reactions that occur when cement and water are combined. This heat release is a highly relevant factor with various effects on the production and use of concrete.
The magnitude of the heat of hydration generated primarily depends on the chemical composition of the cement. Meanwhile, the rate at which this heat is generated is influenced by the fineness of the cement, curing temperature, and its inherent chemical composition.
The chemical hydration reactions of cement are characterized as exothermic, meaning they release heat. This release of energy can reach up to 500 joules per gram (equivalent to 120 calories per gram). Since concrete exhibits low thermal conductivity, it becomes an insulating material. In voluminous concrete structures, the hydration process can induce a significant increase in internal temperature. However, the external surface of the concrete may dissipate some of the heat, resulting in a thermal gradient. During the subsequent cooling of the concrete core, cracks of significant size can occur. This aspect is particularly important in large structures, where the speed and amount of heat generated are determining factors. In the absence of efficient heat dissipation, a high temperature increase in the concrete may occur, along with the risk of thermal expansion.
On the other hand, the heat released during hydration can be beneficial to prevent the freezing of water in the concrete capillaries when used in cold environments. However, it could also lead to undesirable contractions and tensions during the subsequent cooling of hardened concrete at room temperature, causing a phenomenon known as setting shrinkage.
When considering the selection and proper use of cement, it is essential to weigh the heat-generating properties of different cement varieties. Understanding how various types of cement release heat during the hydration process contributes to making the ideal choice for each application, avoiding problems associated with excessive or insufficient heat release under different environmental and construction conditions.
If low heat of hydration is desired, a “low heat of hydration” type can be used, as seen in the post on Cement: Everything You Need to Know.
Volumetric Stability
This concept refers to the ability of cement to maintain a relatively constant volume after completing the setting and hardening process. Volumetric stability is crucial to ensuring the integrity and durability of structures built with cement.
The term “expansive cement” is used to describe cement that undergoes significant expansion after the setting process. This defect is highly problematic, as it can severely compromise the quality and safety of structures built with such cement.
The cement paste, once it has set and hardened, should maintain its volume as much as possible. This is crucial because abrupt changes in volume can lead to internal stresses in the material. In situations where there is considerable volumetric change, such as significant expansion, internal stresses can be high enough to cause the fracture of the hardened material. These expansions can arise due to delayed or slow hydration reactions or the reactivity of compounds present in hardened cement, such as CaO (calcium oxide), MgO (magnesium oxide), or CaSO4 (gypsum).
The volumetric stability of cement is essential for the integrity of concrete and mortar structures. Excessive expansion issues can jeopardize the durability and safety of constructed works. Therefore, it is crucial to select and carefully use cements that exhibit adequate volumetric stability and minimize the risks associated with uncontrolled changes in material volume.
Cement Strength
The mechanical strength that cement acquires once it has hardened is undoubtedly one of the most prominent characteristics regarding its requirements for structural applications. Therefore, it is not surprising that strength evaluations play an essential role in all cement-related specifications.
The ability of a mortar or concrete to bear loads lies in the inherent cohesion of the cement paste, its ability to adhere to aggregate particles, and to some extent, the strength of the aggregate used.
Direct strength tests are not conducted on pure cement paste, primarily due to the experimental complexities surrounding the molding process, which could lead to substantial variability in the results obtained. Instead, to assess cement’s strength, mortars are used. These mortars consist of a specific mixture of water, cement, and fine aggregate, and they are prepared following precise procedures under strictly controlled conditions.
Various testing methods are used to measure strength, such as direct tension tests, direct compression tests, and bending tests. In particular, bending tests are used to determine the tensile strength, as it is widely accepted that cement paste exhibits significantly higher strength in compression than in tension.
NOTE: The tests and assays specified in the post are governed by the Colombian technical standards (NTC); they may vary depending on the country.
References
NTC 121 and 321: Relevant technical standards for Portland cement specifications.
NTC 221: A technical standard that describes the method for evaluating the density of cement using the Le Chatelier flask.
NTC 226 or 294: Technical standards that establish methods for determining the fineness of cement through sieving.
NTC 33: A technical standard that describes the use of the Blaine permeameter to measure the fineness of cement.
NTC 597: A technical standard that describes the use of the Wagner turbidimeter to measure the fineness of cement.
NTC 110: A technical standard that establishes the procedure for determining the normal consistency of cement paste using the “Vicat” device.
About The Author
Samuel Parariá
Estudio: University of Francisco de Paula Santander.
Major: Civil Engineering.
Favorite Areas: Structures, Traffic Engineering, and Road Design.
Location: Cúcuta, Norte de Santander, Colombia.
Related
Pavers in Civil Engineering
What are the Non-Mechanical Properties of Materials in Civil Engineering?
Mechanical Properties of Materials (under construction)